Rubber Track Tread System for Agricultural Tractors, Harvesters, and Farm Machinery
Better Traction, Flotation, and Stability
Buying is easy:
Contact us and we will deliver it to you.
Internal Structure of Rubber Track Layers
Our tracks have a 4-layer structure, designed to maintain dimensional stability and protect them from cuts, tears, and impacts.
Surface Layers
The external layers of the track, made of high-strength rubber, withstand contact with the ground and traction mechanisms. They provide grip, traction, and durability, optimizing self-cleaning and reducing wear.
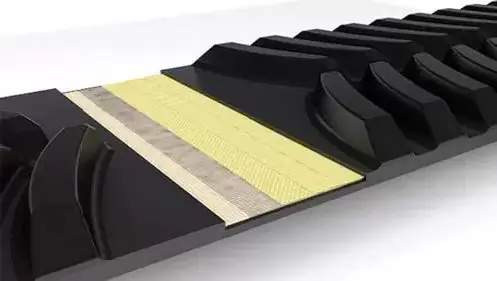
Angular Layers
The angular layers, arranged obliquely, improve the lateral stability of the track. They evenly distribute the load and maintain structural integrity against lateral forces, such as those generated when turning or operating on sloped terrain.
Reinforcement Layer (Metalcable)
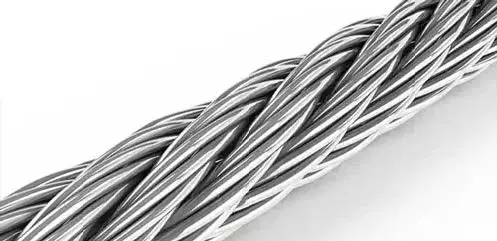
It is composed of spiral metal wires, providing high tensile strength and preventing stretching or breakage under heavy loads. The standard diameter in our tracks is 6.3 mm.
Lateral Layer
The fourth layer is located on the inner side of the tread, protecting the edge in contact with the wheels and drive rollers. In addition to impact protection against stones and hard objects, it provides structural support for heavy machinery.
Model Catalog
CAT CHALLENGER 35/45/55
- 18 Inches 457X152.4X53CC
- 25 Inches 635X152.4X53CC
- 30 Inches 762X152.4X53CC
JOHN DEERE 8000T
- 16 Inches 406X152.4X54JD
- 18 Inches 457X152.4X54JD
- 25 Inches 635X152.4X54JD
- 30 Inches TF762X152.4X54JD
QUADTRAC/CASE IH 400-600
- 30 Inches 762×152.4×42
- 36 Inches 915X152.4X42
JOHN DEERE HARVESTER S690
- 25 Inches 26″x6″x39″(660х152.4)
CAT CHALLENGER 65/75/85/95
JOHN DEERE 8 RT
- 16 Inches TF406X152.4X59JD
- 18 Inches TF457X152.4X59JD
- 25 Inches TF635X152.4X59JD
- 30 Inches TF762X152.4X59JD
CLASS LEXION 600
- 25 Inches 635*152.4*44
AGCO CHALLENGER MT 700
JOHN DEERE 9000T
- 30 Inches TF762X152.4X63JD
- 36 InchesTF915X152.4X63JD
Warranty
The ASMtrack product line comes with a 2-year or 1,500-hour warranty. This policy is fair and precise, as it is based on the track wear formula over time.
IMPORTANT: For 2 years, we provide a warranty on the tracks, but the claimable amount decreases as the track wears out.
How Agricultural Rubber Tracks and Treads Are Manufactured:
Guide Block Density
The engineers at ASMtrack focus on quality and durability.
First and foremost, it is important to highlight that a greater number of guide blocks have been incorporated into the traction belt. As a result, each individual block bears less load, leading to an increased lifespan and enhanced durability of the track.
The engineers at ASMtrack focus on quality and durability.
First and foremost, it is important to highlight that a greater number of guide blocks have been incorporated into the traction belt. As a result, each individual block bears less load, leading to an increased lifespan and enhanced track durability.
ASMtrack Tracks
Our guide blocks are molded directly onto the internal framework. This prevents them from breaking, especially when used regularly on uneven terrain or when working on slopes.

Other Tracks
In this case, the guide blocks are “glued” onto the track’s framework. When moving on curved paths or slopes, these blocks tend to detach.
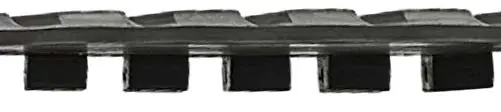
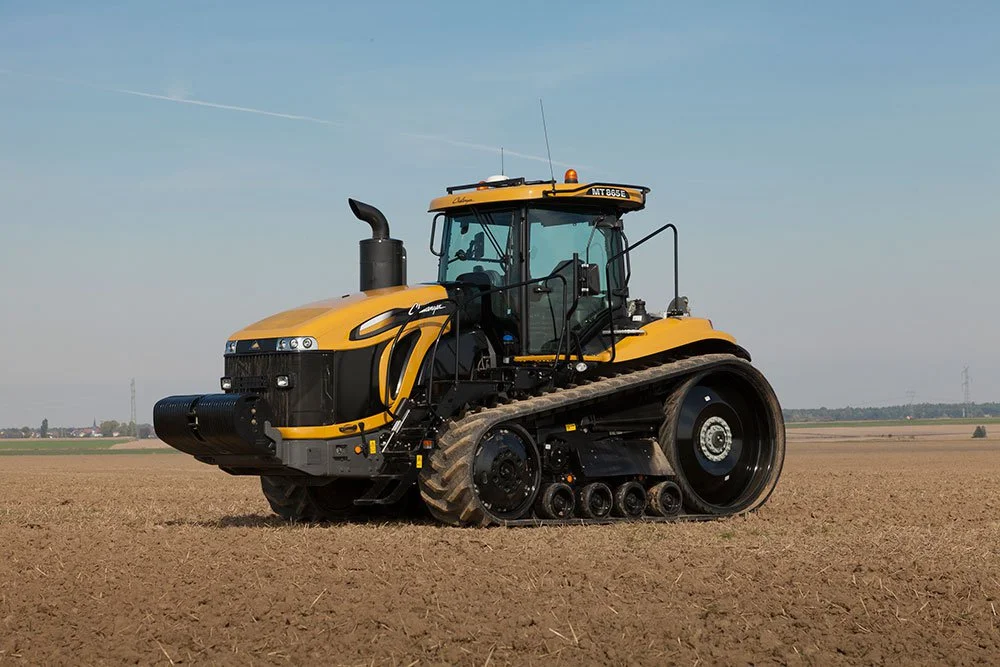
Rubber Tracks: Advanced Tread and Track Systems for Agricultural Machinery
-
Especially in regions with frequent torrential rains, where the soil becomes completely impassable afterward.
They minimize soil compaction in the upper layers, significantly accelerating crop growth and positively impacting yield increases.
To avoid soil damage and prevent work delays, the best solution is to equip your machinery with rubber tracks.
Treads for Tractors, Harvesters, and Agricultural Machinery: Why Choose ASMtrack Rubber Tracks?
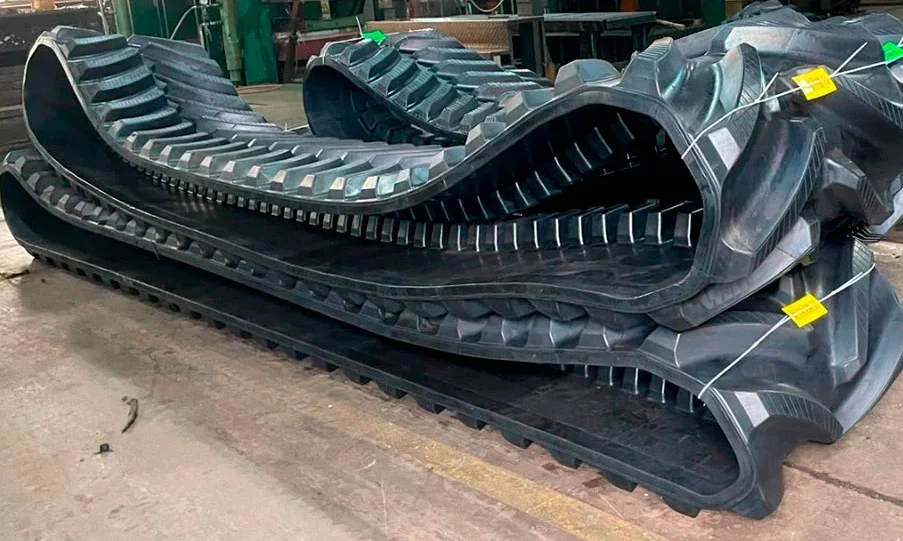
When selecting tracks, a crucial factor is the material composition. ASMtrack uses a combination of natural and synthetic rubber, providing a significant advantage over tracks made solely from synthetic polymers, especially in demanding operating conditions.
Rubber tracks for tractors must have a high durability reserve. This coating can withstand heavy field loads and will not tear upon contact with foreign objects. This is further reinforced by metal cable layers and a robust 42 mm internal frame.
Advantages of Rubber Tracks for Tractors
The wheels of modern agricultural machinery are often heavier than track systems. Additionally, due to their narrow pressure line, wheels tend to compact and damage the upper soil layers.
In contrast, rubber track systems offer several significant advantages:
- Weight Reduction: In many cases, replacing rear wheels with rubber tracks can result in lower overall weight, especially for medium-sized tractors.
- Weight Distribution: Rubber tracks evenly distribute the tractor’s weight over a larger surface area, reducing soil compaction.
- Operational Efficiency: Lower weight and better distribution can lead to improved tractor performance and reduced fuel consumption.
Replacing rear wheels with rubber tracks not only helps reduce the tractor’s total weight, but also improves efficiency, minimizes soil damage, and lowers fuel costs.
Watch video on YouTube