Analysis of Failures in Sheet Metal Wheels of Planters
The Causes of Failures in Planter Wheels
Sheet metal wheels used in planters are subjected to various stresses during operation, which can lead to structural failures. In this analysis, we investigate the main causes of these failures, including a hypothesis provided by a manufacturer highlighting the impact of notches and excessive load on depth control wheels.
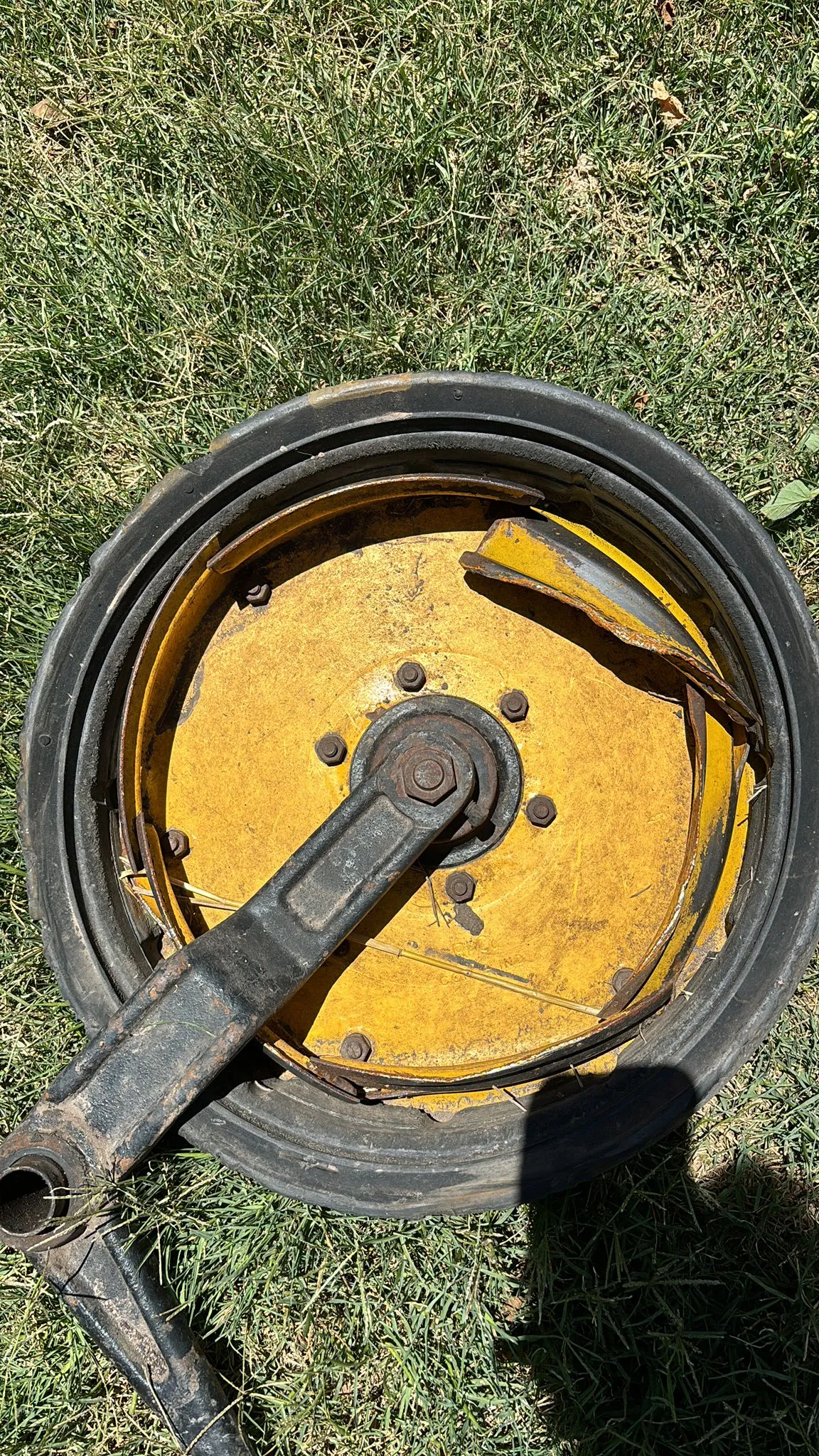
Cause | Description |
1. Overload or Excessive Weight | The half rim may have been subjected to a weight greater than it was designed to handle, leading to its failure. |
2. Strong Impacts | Hits against rocks, roots, or obstacles in hard terrain during use could have caused cracks that eventually resulted in failure. |
3. Material Weakening | Wear, corrosion, or lack of maintenance may have weakened the material, making it more prone to failure. |
4. Manufacturing Defects | A flaw in material quality or errors during the manufacturing process created a weak point that gave way under stress. |
5. Improper Assembly or Adjustment | Incorrect installation or loose bolts may have created uneven pressure on the half rim, leading to its failure. |
6. Material Fatigue | Constant use in adverse conditions, such as rough or abrasive terrain, caused microcracks that gradually expanded and led to failure over time. |
1. Notches as Stress Concentration Points
In the provided photograph (Figure 1), notches can be seen on the rim edge, which act as structural weak points.According to the manufacturer, these notches are no longer included in current designs due to their tendency to concentrate stress under load.
Impact of Notches:
- During operation, notches can accumulate stress due to the cyclic forces and vibrations of the planter.
- These concentrated stresses can lead to cracks and failures, especially under uneven terrain conditions.
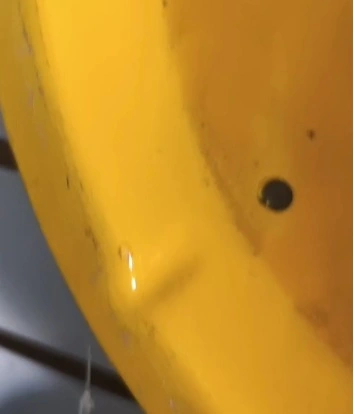
Overload – Fatigue Failure of the Material
On one occasion, we faced a similar problem due to excessive pressure applied to the leveling wheels. When these wheels bear too much load, the rim, often the weakest point, ends up breaking due to material fatigue. This could potentially be the most likely cause.Material Fatigue
Continuous use of agricultural machinery on uneven or abrasive terrain generates cyclic stresses that cause microcracks in weak points of the material. These cracks, initially small, expand with each usage cycle due to material fatigue, further aggravated by surface wear under abrasive conditions.Microcracks
Another probable cause could be related to the material of the wheels. In some cases, rims may develop microcracks in specific areas due to the stamping process. These cracks, though initially imperceptible, can worsen with continuous work and pressure, eventually leading to failure. This issue may also be linked to the quality or thickness of the sheet metal used in their fabrication.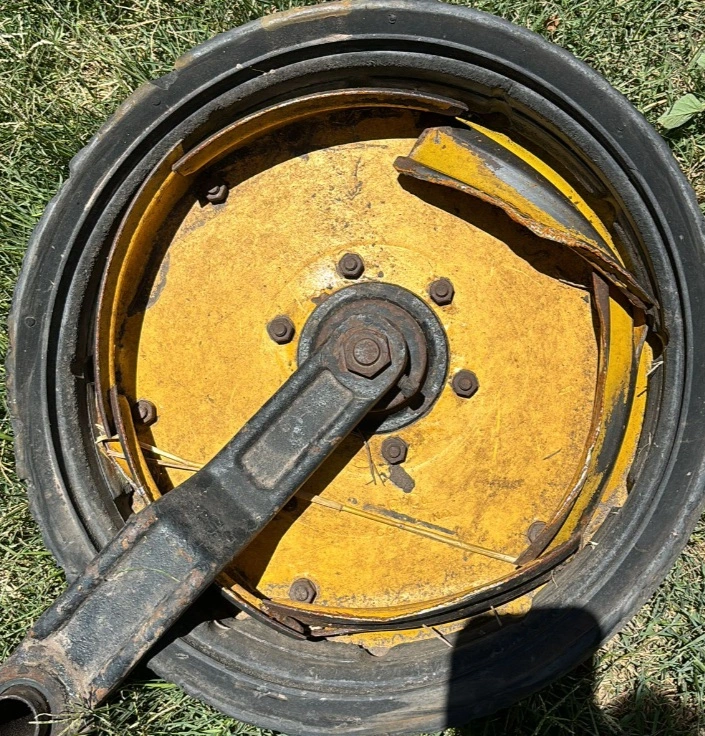
General Observations
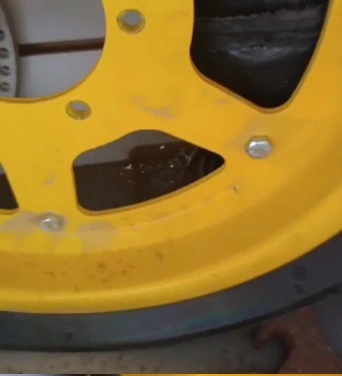
The manufacturer states that the combination of notches (older design) and excessive load on the wheels has been the main cause of these failures. This aligns with previous observations on material fatigue and overload on the rims..
The manufacturer states that the combination of notches (older design) and excessive load on the wheels has been the main cause of these failures. This aligns with previous observations on material fatigue and overload on the rims.
3. Other Factors Contributing to Failures
In addition to notches and excessive adjustment, other factors to consider include:- Material Fatigue: Prolonged use under vibrations and dynamic loads contributes to deterioration.
- Corrosion: Exposure to humid environments and agricultural chemicals can weaken the rim structure.
- Impacts or Use on Uneven Terrain: Increases localized stress on the weakest areas.
Solutions to Prevent Rim Failures
- Rim Redesign: Elimination of notches in newer designs, reducing stress concentration points.
- Preventive Maintenance: Regular inspection of rims to detect cracks or corrosion before total failure occurs.
- Operator Training: Educating operators on proper practices to avoid overloading and to maintain equipment in optimal condition.
Conclusion
Failures in sheet metal rims of planters result from a combination of factors, including notches in older designs and dynamic stresses under intensive use. Incorporating improved designs and precise adjustments are key steps to prevent future failures.